2017 Scm System TC 1350 BT44CC RRD+RRD
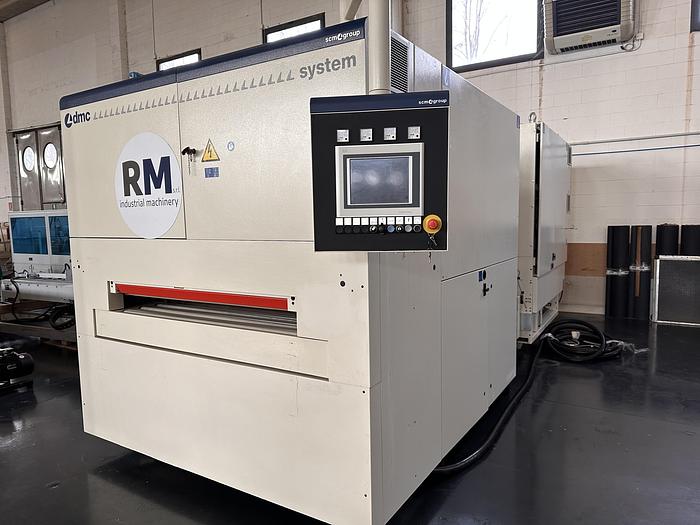
Specifications
Manufacturer | Scm |
Model | System TC 1350 BT44CC RRD+RRD |
Year | 2017 |
Stock Number | MGR010 |
Description
D) Compact line for sanding calibration SOTTO/SOPRA mod. SYSTEM BT44CC 1350 RRD + RRD LOWER GROUPS MOD. B4C 1350 RRD BASEMENT * Fixed workpiece passage height at 900 mm from the ground * Insertion of ribbons from the left side of the machine * Main engines inside the base ADVANCEMENT BENCH * Motorized adjustment of the work surface with two-speed gear motor * Rear rubber-coated carpet drive roller * Device for automatic centering of the conveyor belt * Input safety microswitch for excess thickness * Useful working widths 1350 mm * Min. thickness and max. workable 3 ÷ 170 mm * Feed speed from 3.5 to 18 m/min OPERATING GROUPS * Belt oscillation with electronic control * Automatic disc brakes for quick stopping of groupsets PRESSURE SETS * Inlet grooved rubberized roller equipped with safety device to prevent pieces from returning ELECTRICAL EQUIPMENT * Automatic star/delta starting on the main engine * Magnetothermic protections on motors * Stabilized current power supply for electronic equipment "Hydra V-Pad" CONTROL PANEL * PLC terminal with color LCD display" * Touch screen functionality * Graphic display of the machine configuration * Machine management from touch screen, manually or through 120 configurable work programs by the user * Engagement/disengagement in working position and timing of the roller groups * Management and control of the belt advancement speed * Management and control of the working thickness * Automatic sequential ignition of the main engines * Activation and control of the timing of the belt cleaning blowers * Management of the windowed piece recognition program * Machine operation report (working hours/on hours) * Management of machine failure alarms and fault diagnosis on the electronic boards * Management of machines in compact line configuration EMERGENCIES / SAFETY * Hand protection strap at entry of pieces * Front and rear emergency mushroom switch * Lockable main switch * Automatic emergency stop of the machine in case of: - breakage of the abrasive belt - non-tensioned abrasive belt - lateral exit of the abrasive belt - opening of the access doors to the operating groups - lack of compressed air - motor overload SY B4C 1350* CARRYING BASE * * Control panel on the machine 1st OPERATING GROUP “R” R-CL 1350 * Calibrator/sanding roller assembly The group is equipped with: * Adjustment of the working position of the roller with indicator and pre-selection memory of the abrasive belt grain * Automatic disc brake for stopping the sanding belt in case of emergency * Automatic oscillation of the abrasive belt via electronic system * Abrasive belt rotating in the opposite direction to the advancement - Development of abrasive belt 1900 mm R250 Roller with a diameter of 250 mm R85 85 sh rubber coated calibrator roller with abrasive belt speed of 24 m/sec Pneumatic ON/OFF of the roller made with a pneumatic activation cylinder complete with micrometric adjustment of the position of the roller depending on the thickness of the abrasive belt Oscillating blower for cleaning the longitudinal abrasive belt The device is equipped with: - Operation of the swing with electronic system - Timed intervention activated directly by the piece being processed - Filter and pressure regulator 11 kW (15 HP) motor 2nd OPERATING GROUP “R” R-CL 1350 * Calibrator/sanding roller assembly The group is equipped with: * Adjustment of the working position of the roller with indicator and pre-selection memory of the abrasive belt grain * Automatic disc brake for stopping the sanding belt in case of emergency * Automatic oscillation of the abrasive belt via electronic system * Abrasive belt rotating in the opposite direction to the advancement - Development of abrasive belt 1900 mm R250 Roller with a diameter of 250 mm R65 65 sh rubber coated calibrator/sander roller with abrasive belt speed of 18 m/sec Pneumatic ON/OFF of the roller made with a pneumatic activation cylinder complete with adjustment micrometric of the position of the roller as a function of the thickness of the abrasive belt Oscillating blower for cleaning the longitudinal abrasive belt The device is equipped with: - Operation of the swing with electronic system - Timed intervention activated directly by the piece being processed - Filter and pressure regulator 11 kW (15 HP) motor 3rd OPERATING GROUP “D” DP 4/16 1350* TRANSLATING PLANETARY GROUP WITH 4 HEADS ROTARY ABRASIVE BRUSH HOLDER Prepared for housing 16 brush discs with a diameter of 125 mm. SI/8/125 * Set of 16 rotary discs with a diameter of 125 mm SI/8/125 * Complementary set of 16 discs with a diameter of 125 mm Electronic auto-set of the "DP 4/16" group for work positioning managed by the Hydra V-Pad electronic control 4th OPERATING GROUP “b” GS/200 1350 * BRUSH ASSEMBLY The device is equipped with: - Dust extraction hood - Adjustment of the working position of the roller - Rubberised pressure roller at entry and exit Cleaning roller with a diameter of 200 mm in Tampico 1.1 kW (1.5 HP) main motor · PRESSERS GP/M-E Pressure group with rubberized rollers and tip at entry to the 1st roller group GP/M-I Pressure group with rubberized rollers and intermediate tip between the 1st and 2nd roller group GP/M-U Pressure group with rubberized rollers and tip exiting the 3rd roller group · WORK PLAN Carpet advancement with 3 kW inverter 60 sh rubber conveyor belt · COMPACT IN-LINE MACHINE DEVICES Machine in compact start-of-line version (lower/upper) with System T4C 1350 following. The entire compact line is managed by a single "Hydra V-Pad" control panel and a single "PLC" ELECTRONIC CONTROL 10.4" touch-screen monitor for Hydra V-Pad PLC X-20 control panel Modular hardware structure for managing machine functions from the "Hydra" control panel. UPPER GROUPS T4C 1350 RRD BASEMENT * Insertion of ribbons from the left side of the machine * Main engines inside the base ADVANCEMENT BENCH * Motorized adjustment of the work surface with two-speed gear motor * Rear rubber-coated carpet drive roller * Automatic device for centering the conveyor belt * Input safety microswitch for excess thickness * Useful working width 1350 mm * Min. thickness and max. workable 3 ÷ 170 mm * Feed speed from 3.5 to 18 m/min OPERATING GROUPS * Belt oscillation with electronic control * Automatic disc brakes for quick stopping of groupsets PRESSURE SETS * Inlet grooved rubberized roller equipped with safety device to prevent pieces from returning ELECTRICAL EQUIPMENT * Automatic star/delta starting on main engines * Magnetothermic protections on motors * Stabilized current power supply for electronic equipment EMERGENCIES / SAFETY * Hand protection strap at entry of pieces * Front and rear emergency mushroom switch * Lockable main switch * Automatic emergency stop of the machine in case of: - breakage of the abrasive belt - non-tensioned abrasive belt - lateral exit of the abrasive belt - opening of the access doors to the operating groups - lack of compressed air - motor overload BASIC MACHINE SY T5C 1350 * CARRYING BASE * * Control panel on the machine 1st OPERATING GROUP “R” R-CL 1350 * Calibrator/sanding roller assembly The group is equipped with: * Adjustment of the working position of the roller with indicator and pre-selection memory of the abrasive belt grain * Automatic brake for stopping the sanding belt in case of emergency * Automatic oscillation of the abrasive belt via electronic system * Abrasive belt rotating in the opposite direction to the advancement - Development of abrasive belt 1900 mm R250 Roller with a diameter of 250 mm R85 85 sh rubber coated calibrator roller with abrasive belt speed of 24 m/sec Pneumatic ON/OFF of the roller made with a pneumatic activation cylinder complete with adjustment micrometric of the position of the roller as a function of the thickness of the abrasive belt Oscillating blower for cleaning the longitudinal abrasive belt The device is equipped with: - Operation of the swing with electronic system - Timed intervention activated directly by the piece being processed - Filter and pressure regulator 11 kW (20 HP) motor 2nd OPERATING GROUP “R” R-CL 1350 * Calibrator/sanding roller assembly The group is equipped with: * Adjustment of the working position of the roller with indicator and pre-selection memory of the abrasive belt grain * Automatic brake for stopping the sanding belt in case of emergency * Automatic oscillation of the abrasive belt via electronic system * Abrasive belt rotating in the opposite direction to the advancement - Development of abrasive belt 1900 mm R250 Roller with a diameter of 250 mm R65 65 sh rubber coated calibrator/sander roller with abrasive belt speed of 18 m/sec Pneumatic ON/OFF of the roller made with a pneumatic activation cylinder complete with adjustment micrometric of the position of the roller as a function of the thickness of the abrasive belt Oscillating blower for cleaning the longitudinal abrasive belt The device is equipped with: - Operation of the swing with electronic system - Timed intervention activated directly by the piece being processed - Filter and pressure regulator 11 kW (15 HP) motor 3rd OPERATING GROUP “D” DP 4/16 1350* TRANSLATION GROUP WITH 4 ROTARY HEADS HOLDERING ABRASIVE BRUSHES Prepared for housing 16 brush discs with a diameter of 125 mm. SI/8/125 * Set of 16 rotary discs with a diameter of 125 mm SI/8/125 * Complementary set of 16 discs diameter 125 mm Electronic auto-set of the "DP 4/16" group for work positioning managed by the Hydra V-Pad electronic control 4th OPERATING GROUP “b” GS/200 1350 * OUTPUT BRUSH UNIT The device is equipped with: - Dust extraction hood - Adjustment of the working position of the roller - Rubberised pressure roller at entry and exit Cleaning roller with a diameter of 200 mm in Tampico 1.1 kW (1.5 HP) main motor · PRESSERS GP/M-E Pressure group with rubberized rollers and tip at entry to the 1st roller group GP/M-I Pressure group with rubberized rollers and intermediate tip between the 1st and 2nd roller group GP/M-U Pressure group with rubberized rollers exiting the 3rd roller group · WORK PLAN Carpet advancement with 3 kW inverter 60 sh rubber conveyor belt · COMPACT IN-LINE MACHINE DEVICES Machine in compact end-of-line version (lower/upper) with previous System B5C 1350. The entire compact line is managed by a single "Hydra V-Pad" control panel and a single "PLC" T4M base with worktop at a fixed height of 900 mm from the ground Predisposition for vacuum top (perforated top and carpet) for 2 modules Internal electric fan with 7.5 kW (10 HP) motor for 2 modules N° 4 independent floating shelves to compensate for differences in material thickness